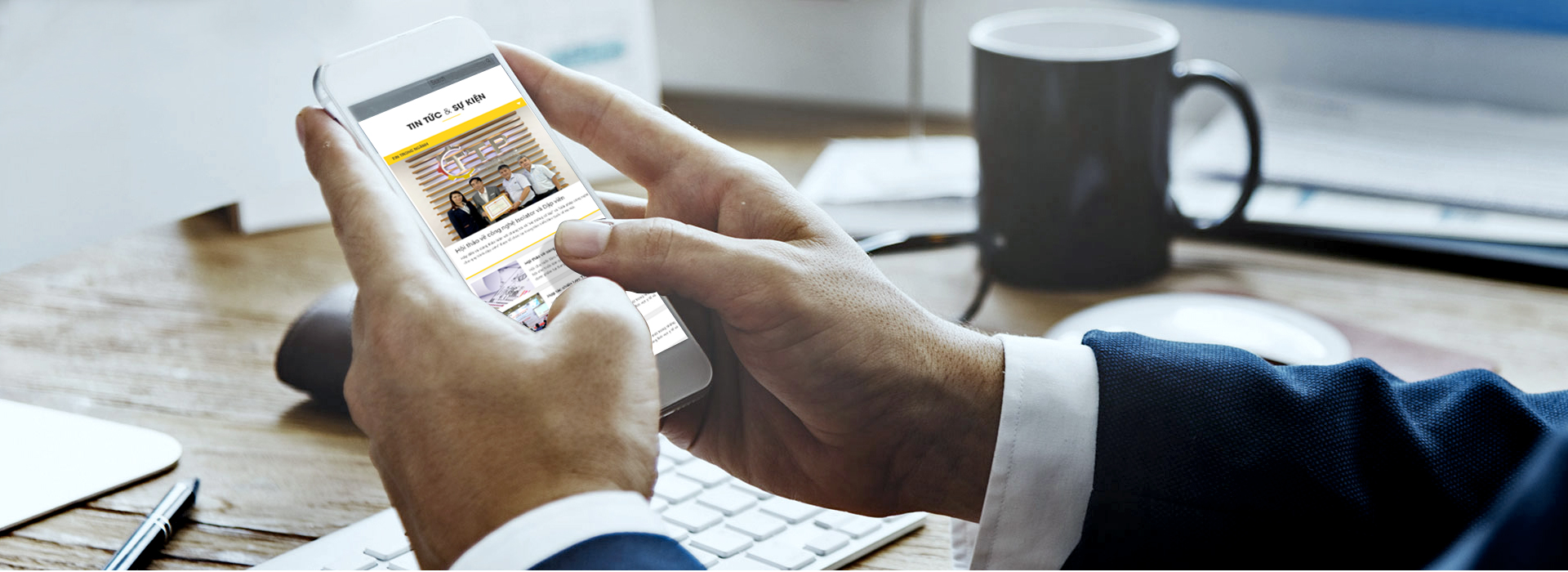
COMMON TABLET DEFECT
COMMON TABLET DEFECT
CAUSES AND CORRECTIVE ACTIONS
1 . Sticking
Cause:
- Punch face condition
- Excessive moisture
- Ambient conditions (temperature and humidity)
- Deficient formulation and/or process
- Punch tips worn, burred or have J-hook present
- Insufficient compaction force
Corrective actions:
- Polish punch faces/consider matte finish
- Check moisture content of granulation
- Increase compaction force
- Rework/replace punches
- Picking
Cause:
- Punch face condition
- Excessive moisture
- Ambient conditions (temperature and humidity)
- Deficient formulation and/or process
- Punch tips worn, burred or have J-hook present
- Insufficient compaction force
- Poor embossing design
Corrective actions:
- Polish punch faces/consider matte finish
- Check moisture content of granulation
- Increase compaction force
- Rework/replace punches
- Redesign embossing (consider pre-pick islands
and taper peninsulas of embossing)
- Lamination
Cause:
- Air Entrapment
- Excessive pre-compression
- Excessive main compression
- Ringed (worn) die bore
- Punch tips worn, burred or have J-hook present
- Excessive fines
Corrective actions:
- Compress higher in die
- Taper die
- Reduce pre-compression
- Reduce main compression
- Reverse or replace die
- Capping/ Splitting
Causes
- Air Entrapment
- Excessive pre-compression
- Excessive main compression
- Ringed (worn) die bore
- Punch tips worn, burred or have J-hooks present
- Excessive fines
- Poor granulation ( too dry)
Corrective actions
- Compress higher in die
- Taper die
- Reduce pre-compression
- Reduce main compression
- Reverse or replace die
- Reduce fine
- EDGE EROSION
Causes
- Unequal distribution of granulation in die bores
- Particle segregation or stratification in hopper
- Low moisture content
- Poor tablet design
- Poor compaction
Corrective actions
- Ensure raw material quality
- Balance/level tablet press
- Set scraper correctly
- Minimize fill depth
- Redesign tablet geometry
- EXCESSIVE FLASHING
Causes
- Punch tips worn, burred or have J-hook present
- Worn die bore/excessive clearence
- Excessive fines
Corrective actions
- Rework/replace punches
- Reverse or replace die
- Reduce fines
- Discoloration
Causes
- Excessive pressure
- Poor tablet design
- Formulation component readily oxidized
Corrective actions
- Reduce main compression force
- Evaluate tablet design
- Identify discoloration and take corrective action
- Dark spec
Causes
- Excessive pressure
- Poor tablet design
- Formulation component readily oxidized
Corrective actions
- Reduce main compression force
- Evaluate tablet design
- Identify discoloration and take corrective action
- SCORCHED BELLY BAND
Causes
- Excessive pressure
- Poor tablet design
- Formulation component readily oxidized
Corrective actions
- Reduce main compression force
- Evaluate tablet design
- Identify discoloration and take corrective action
- Chipping
Causes
- Punch tips worn, burred or have J-hook present
- Poor tooling design
- Upper punch misalignment
Corrective actions
- Rework/replace punches
- Preload shaped tooling properly during
installation
- Inspect turret for excessive punch guide wear,
- key-way wear and die pocket wear
- DOUBLE IMPRESSION
Causes
- Inconsistent lower punch flight
- Granulation lost/gained after dosing
- Overfilled/under-filled feeder
- Worn/improper scraper adjustment
- Non-uniform lower punch lengths
Corrective actions
- Add keys on round punches
- Use punch retainers/brakes
- THICKNESS/WEIGHT DEVIATION
Causes
- Free rotation of either upper or lower punch
After pre-compression
After main compression
During tablet ejection
Corrective actions
- Check/replace lower punch retainers
- Check/replace lower punch scraper seals
- Adjust feeder speed
- Reduce recirculated powder
- Check/replace scraper
- Check lower punch working lengths
Conclusion
One conclusion that you should draw from this article is that tablet press defected can be caused by one or more reasons. Environmental and design factors can affect how well a pill will form. Some products are very sensitive to temperature and humidity, so they may compress differently or not at all according to the slightest change in the environment. If you're the troubleshooter in charge of solving an existing problem, assess the problem at the outset and work it out at an earlier stage. Research all process problems and record as much data as possible. Finally, if you do make changes, try to make just one change at a time. This will help you associate each change with a result.