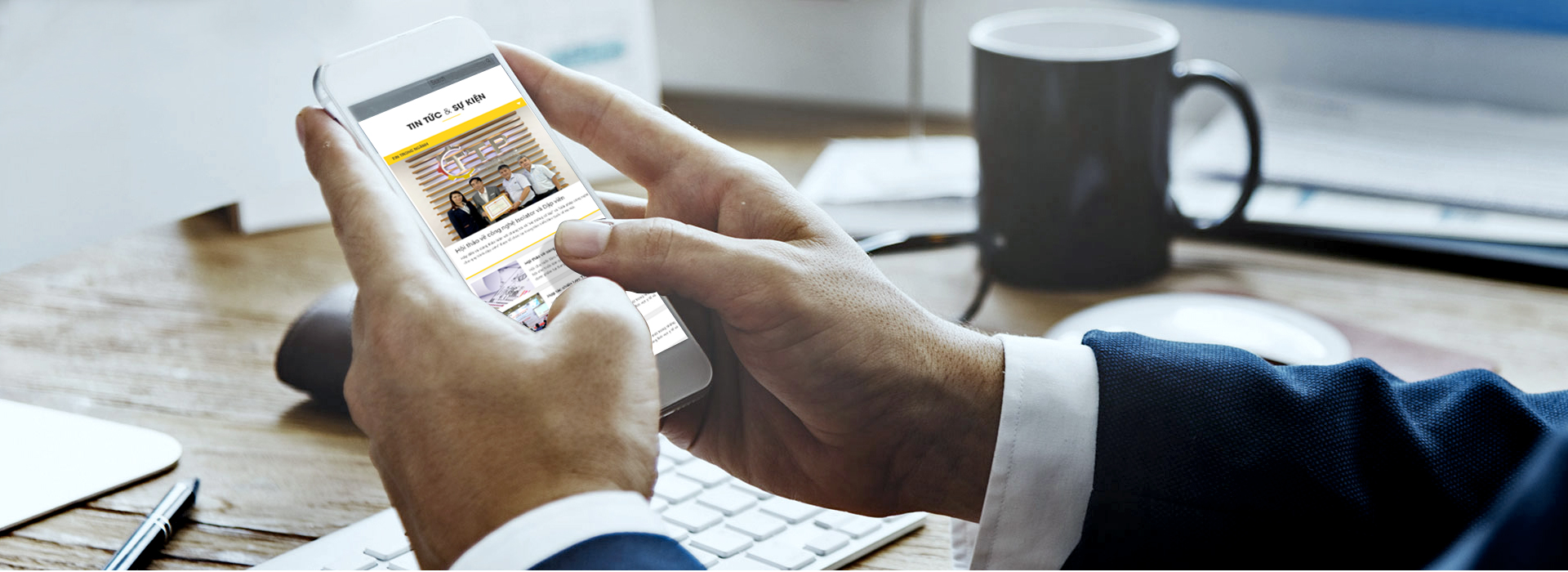
WHAT CAN WE DO TO SPEED A TABLETED DRUG PRODUCT TO MARKET?
A: Charles N. Kettler, Natoli Scientific, a division of Natoli Engineering, says: Sticking and picking are common in manufacturing tableted drug products, and concerns about reaching the market quickly can lead to hasty decisions and unanticipated compression problems during scale-up. Often the design process for a tablet overlooks seemingly minor details of tablet design, which can result in defects when the scale of manufacture increases from R&D to full production
When developing a tablet, manufacturers often leave people from important departments out of early meetings. Marketing, product development, engineering, and production staff all need a seat, and you should also include your tooling vendor. Before you make any final decisions, answer five important questions:
- Given the tablet's intended shape and size, what tooling configuration will the product require?
- How will the tooling configuration of the cup affect the compression force required to compress the tablet?
- Are any components of the formulation prone to sticking and/or picking?
- Are any components sensitive to the heat of standard operating temperatures?
- Is the product abrasive or corrosive?
These details are essential to the tablet and tooling design to meet your tablet's exacting requirements. Identifying some problems before finalization of tablet and tooling designs can reduce the challenges that you and your tooling provider share. For example, early decisions about tablet edges and fonts, about whether to pre-pick or taper potentially troublesome areas of punch engraving, and about steel types and coatings can aid in a speedier introduction of a drug product to market.
Tablet edges
Simply modifying the edge of a tablet from a flat-faced bevel edge (FFBE) to a flat-faced radius edge (FFRE) can support the efforts of both marketing and production. The FFRE's softer appearance and smoother mouth-feel can reduce anxiety in some patients, increasing patient acceptance. The FFRE tooling design also reduces strain and wear on punches during manufacturing, meaning you can produce more tablets with a single set of tools and lower operating costs associated with a product.
Additionally, the FFRE design reduces chipping and edge erosion, which can occur with the FFBE. The FFBE design has sharper edges that result in faster tooling wear, and its use requires more frequent inspection and polishing of tools. The radius edges on the FFRE design also increase the strength of the finished tablet. In Figure 1, note the differences in the transition angles around the face of the tablets for the sharp, 0.015 inch radius angle of the FFBE compared to the smoother, 0.060 inch radius angle of the FFRE. /
Font selection
Font selection is often a battle of form versus function. While an ornate or decorative font may be pleasing to the eye, it is more likely to cause picking problems and tablet defects. Figure 2 illustrates an impractical font where picking issues are more likely to occur. The variation in engraving depth and width as well as the isolated and unnecessary peninsulas on the letters are impediments to even powder compaction, as Figure 2 indicates in the shaded areas. That variation often leads to powder picking away from the core of the compressed tablet. Figure 3 illustrates the same embossing with a more practical font that uses engraving and corner radii, minimizing picking and allowing consistent powder compaction.
Pre-pick and taper
You should pay attention to the design of the engraving cut. To reduce or eliminate problems with picking, you can incorporate pre-picking in the embossing design. It reduces the depth of the engraving for the formation of the island. Figure 4 illustrates the reduction of the engraving for the island on the number "9" from 0.33 millimeter to 0.17 millimeter, which is a 50 percent pre-pick. The reduction can range from 10 to 100 percent depending on the extent of the picking problem. For branding or aesthetic purposes, you should further consider whether you are coating tablets post-compression, because excessive pre-pick can significantly reduce the clarity of the logo. /
Other characters that don't have fully enclosed areas are also prone to picking. Letters like E, S, K, and M, and numerals like 2, 3, and 5 all contain partially enclosed areas that are described as peninsulas. For these areas, employ a feature called tapering or ramping to prevent picking. This feature tapers downward, toward the enclosed end of the peninsula by a percentage of the engraving depth. Peninsulas often taper between 10 to 50 percent of the engraving depth, with 30 percent being the most common. An example of 50 percent taper is illustrated on the right side in Figure 5.
Steel types and coatings
If you discover sticking and picking during the R&D stage or want to resolve such issues when you are ordering your next set of punches for a product with known sticking and picking, consider a specialty steel. It is widely accepted that punch steel with a high concentration of chromium in the alloy chemistry, usually from 16 to 18 percent, enhances the release of a compressed product. A reputable tooling vendor will have multiple grades of high-chrome steel from which to manufacture the punches. Several other specialty steels are also available that can enhance the performance and service life of the punches and dies with regard to compressive strength, wear resistance, and corrosion resistance.
Ultimately, several remedies can help speed a new drug to market, ranging from slight formulation changes to major modifications of tablet design and tooling. When developing a to-market strategy, consult your tooling vendor early in the process. The company's insights can benefit your final product and assist in creating a tablet that both the manufacturer and the end-consumer will accept. Discussing all unique physical properties with your tooling vendor during the tablet-design phase often can eliminate sticking and picking issues before they occur.
Charles N. Kettler, PhD, is director at Natoli Scientific, a division of Natoli Engineering, St. Charles, MO. Kettler has worked in the area of process analytical technology (PAT) for more than 20 years in the chemical and pharmaceutical industries, implementing off-the-shelf and custom-designed measurement systems for process control. In addition, Kettler is currently co-director of the Natoli Institute for Industrial Pharmacy Research and Development at the Arnold and Marie Schwartz School of Pharmacy at Long Island University.
* is a graduate school of Long Island University and Founded in 1886, it is one of the oldest pharmacy schools in the United States today. It became affiliated with LIU in 1929, and was fully merged into LIU in 1976
Source Document: Natoli Engineering Company Inc.